INVENTORY
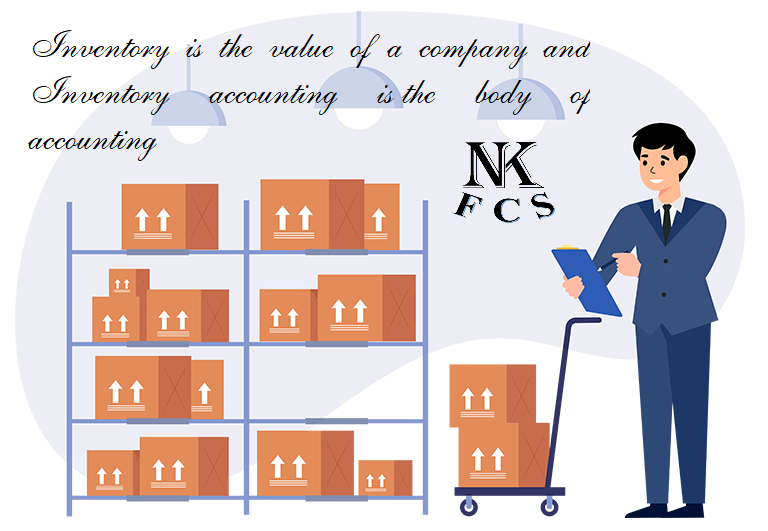
Inventory accounting is the body of accounting that deals with valuing and accounting for changes in inventoried assets.
Inventory management, which involves the efficient control of a company’s inventory including sourcing, storage, sale, and replenishment, is important to a business’s success as it ensures the right materials and products are available to customers while controlling costs. Also, increase market competitiveness, enhance brand reputation, improve productivity, and lower customer costs while generating customer loyalty through consistent availability of products.
Moreover, Inventory control involves various techniques for monitoring how stocks move in a warehouse. Four popular inventory control methods include ABC analysis; Last In, First Out (LIFO) and First In, First Out (FIFO); batch tracking; and safety stock. This section explains how each of these methods functions and how they can support your business.
Inventory control handles existing stock in a warehouse, while inventory management involves the overall movement of goods across supply chains
Some examples of inventory that typically requiring accounting and management include:
Raw materials: The materials a business uses to manufacture a product
Parts and components: The items used in the production of goods, but unlike raw materials, they remain in their original form
End products: Also called finished goods, these are the items a company produces or sells in their completed form
Work-in-progress (WIP): These are items currently in production but not completed by inventory calculation or year-end accounting time
Maintenance and repair supplies: Also called MRO, these are supplies required to ensure maintenance of production systems, physical materials to repair them, and other items required for effective operations
Individual packaging materials: Companies use these materials to wrap or encase a product for sale, like plastic bags for cereal and cardboard boxes for the bagged cereal
Packing materials
Packing materials are items businesses use to ship and package products. Primary packing materials include boxes, bags, and containers stores use to display products in a retail environment. Secondary packing materials are anything companies use for convenient storage and transportation of their products, such as large cardboard boxes. Businesses may also use miscellaneous packing materials to store and transport products, such as bubble wrap, foam peanuts, pallets, and pallet wrap
Safety stock
Safety stock is the excess amount of product a business keeps on hand to meet its regular demands. Keeping safety stock, also known as buffer stock, is essential if there’s a sudden increase in demands, a natural disaster, or a human error interferes with the supply
Decoupled inventory
Assembly processes typically have extra inventory, known as decoupled inventory, for each stage of the manufacturing process to prevent potential work stoppages. Decoupled inventories help prevent delays during manufacturing by allowing employees to continue working even if the earlier stages encounter difficulties
Smoothing inventory
A smoothing inventory, also known as anticipation inventory, means purchasing and storing products or supplies above the organization’s current needs to prepare for a future event. Companies can purchase smoothing inventory in both the manufacturing and service sectors
Transit inventory
Transit inventories are crucial for companies that ship items from one location to another. Once a company pays for an item, but before a supplier delivers it, it becomes transit inventory
Excess inventory
Any goods or unused raw materials are excess inventory. If the excess inventory is no longer useful, it’s dead inventory or obsolete inventory. When a haircare company has leftover packaging from a limited release, it turns into dead or obsolete inventory
Dead stock
Dead stock is obsolete inventory that a company cannot use or sell to customers. Expired inventory, outdated models of technology, or products released for a specific purpose can cause dead stock
Theoretical inventory
Theoretical inventory refers to the amount of inventory necessary for a company to carry out its daily operations. It’s a hypothetical inventory amount rather than a literal count. A theoretical inventory aims to balance inflows, processing, and outflows into one ideal operation. It describes the average inventory necessary to run a production line
Cycle inventory
Cycle inventory refers to inventory that a business uses and replaces regularly. A cycle inventory aligns inventory and machine setup costs to reduce the total cost of production. To use space efficiently, it’s helpful for companies to know the size of their cycle inventory. This is because it needs sufficient space to store cycle inventory and access it regularly
ABC Analysis
ABC analysis in inventory control classifies stocks based on their importance, price, and sales volume. These criteria determine the number of items a company will bring to the market
LIFO and FIFO
Both inventory control techniques organize how inventory items move in and out of the warehouse based on their arrival date. Priority will depend on the type of products available in the storage facility
Batch Tracking
Batch tracking is also a great way of organizing stock items in a warehouse facility. In this method, goods of the same production date and materials are grouped together
Inventory also talks about:
Source, purchase, and receive raw materials
Check, catalogue, stock, and track items
Take and verify orders
Pick and ship orders
Revise totals and replenish inventory
Monitor data
Types of Inventory Control Systems
Periodic Inventory Control System
The periodic inventory control system pertains to a recurring count of goods at specific intervals. In this system, warehouse managers manually count their inventory on a monthly, quarterly, or annual basis. The exact period depends on an organization’s needs and business activities
Perpetual Inventory Control System
The perpetual inventory control system provides accurate count of inventory levels in real time. It utilizes technology, such as barcodes and Radio Frequency Identification (RFID) tags, for tracking products
Inventory also involves Services:
Maintenance, repair, and operating supplies (MRO)
Service inventory
A business’ service inventory shows the amount of service it can provide over a specific timeframe. As an alternative to standard inventories, service inventories contain data linking the physical capabilities of businesses with their potential services